Circumstance:
- Subassembly components involved technology critical to EPA emission compliance.
- Critical components from 2 different non-US suppliers.
- Needed to track lot information for new components to ESN.
- Component function critical for engine performance.
Action Plan:
- Falcon Manufacturing asked to provide mechanism to track lot information.
- New subassembly process designed by Falcon Manufacturing.
- One piece material flow, fail-safe’s, lot control and product serialization implemented for all parts.
- Worked with Tier II suppliers to modify bar code of incoming material to include lot information.
- Falcon Manufacturing developed software to scan barcode and tie lot information into job order.
- Each subassembly component is given unique serial number.
- Each returnable container is given a unique serial number.
- Barcode information contains serial number, all lot information for components, and all manufacturing data.
- Worked with customer to tie software program into the production line.
- Each subassembly is scanned prior to installation.
- All barcode information is tied to ESN for tracking of all component lot information.
Results:
- Able to track all lot information for overseas suppliers.
- Serialization of parts and containers allowed for quick and efficient containment as design issues were worked through.
- Lot control process, along with scanning at the production line, allowed for design changes to be tracked seamlessly.
- Technologies allowed all parties to be ahead of design
Client | Large Automotive Supplier |
Locationn | Indiana, U.S.A. |
Tipo de Instalaciones |
|
Timeline | RFQ: 2 weeks turnaround Launch: 8 weeks from award date. |
Scope of Work |
|
FALCON MANUFACTURING | 164 Southpark Blvd Greenwood, IN 46143 Phone: 317-884-3600 |
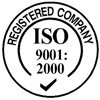
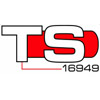